High-Quality Custom Screen Printing for Team Apparel
High-Quality Custom Screen Printing for Team Apparel
Blog Article
Screen Printing Uncovered: Every Little Thing You Required to Learn About Tee and Garment Printing Techniques
If you've ever before wondered how those vivid designs wind up on your favorite t-shirts, you remain in the right location. Display printing is a fascinating approach that incorporates art with strategy, offering endless possibilities for imagination. Recognizing the principles, from tools to ink selections, can considerably impact your results. Prepared to check out the essential elements that make screen printing an art form? Let's discover the details that can elevate your tasks.
The Fundamentals of Display Printing: Just How It Works
When you plunge right into display printing, you'll uncover it's both a science and an art. At its core, screen printing includes creating a stencil, or display, that allows ink to go through only in particular areas (screen printing kit). You begin by selecting your style and preparing your screen with a light-sensitive solution. When you reveal this emulsion to light, it solidifies, leaving your design as an adverse room.
Next, you'll blend your inks and prepare your printing surface. Setting the screen over the material, then utilize a squeegee to push ink through the display onto the garment. This process needs precision, as you desire clear, vibrant prints. After printing, you'll cure the ink with warmth, ensuring it sticks to the textile and lasts through laundries. Each action is necessary, and mastering them will certainly elevate your screen printing skills, changing simple garments right into unique, meaningful items.
Sorts Of Screen Printing Techniques
When you understand the basics of display printing, it's time to explore the various methods that can boost your designs. One preferred approach is standard display printing, where ink is pressed via a stenciled display.
Another option is plastisol printing, understood for its sturdiness and brilliant shades, making it a preferred for numerous brands. Experiment with halftone printing to produce gradient results and detailed layouts.
Crucial Equipment for Screen Printing
To accomplish stunning lead to screen printing, having the appropriate tools is fundamental. You'll require a tough screen printing frame, which holds the mesh that moves your layout onto the garment. Next off, invest in high-quality squeegees; these are important for applying ink evenly throughout the display. You'll also require a great direct exposure system to produce your screens, along with a washout cubicle for cleansing them after usage. A trustworthy warm resource, like a conveyor dryer or warmth press, is crucial for curing your prints to ensure longevity. Do not fail to remember a proper workspace, outfitted with tables and storage space for your materials. Safety equipment, such as masks and gloves, will maintain you safe from chemicals and inks. With the right tools, you'll be well on your means to generating professional-quality prints.
Choosing the Right Inks and Materials
When choosing inks and materials for screen printing, you need to consider the type of ink that works best for your project. Think of fabric compatibility to guarantee your designs look excellent and last long. Likewise, discover environment-friendly ink options to make your printing procedure much more lasting.
Sorts Of Display Inks
Choosing the right display ink is essential for accomplishing vivid, resilient prints that meet your task's demands. There are several types of display inks to analyze. Specialty inks, such as metallic or glow-in-the-dark, can add one-of-a-kind results to your designs.
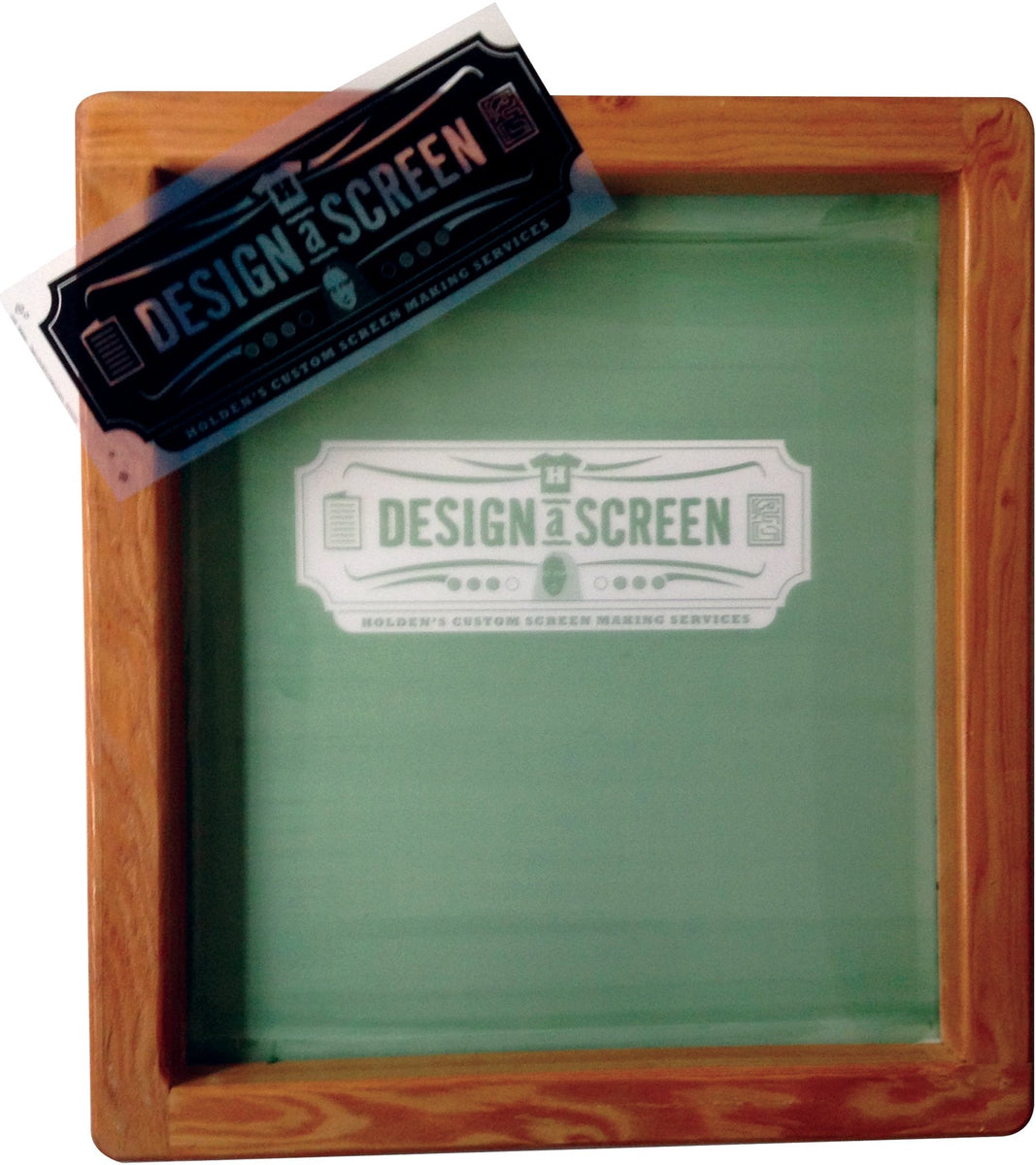
Material Compatibility Factors To Consider
Comprehending fabric compatibility is vital for accomplishing premium screen prints, particularly considering that different products respond uniquely to various inks. When selecting inks, take into consideration the material kind-- cotton, polyester, or blends. For cotton, water-based inks function well, offering softness and breathability. Polyester, on the various other hand, usually calls for plastisol inks for much better adhesion and vibrant shades. You may need to use a combination of both kinds if you're publishing on blends. Always examine your inks on sample material to guarantee they adhere effectively and maintain color stability. In addition, bear in mind that fabric weight and appearance can impact the last outcome, so picking the appropriate ink and material combination is crucial for your project's success.
Eco-Friendly Ink Options
Environment-friendly inks are coming to be a preferred selection for screen printers that want to reduce their ecological impact while keeping high quality. When selecting inks, consider water-based inks, which are much less hazardous and simpler to clean up contrasted to standard solvents.
Furthermore, try to find inks made from renewable energies, such as soy or vegetable-based choices. By picking the appropriate inks and materials, you'll not only produce sensational designs yet additionally add to a more sustainable printing procedure. Make the button, and your prints will certainly reflect your commitment to the setting!
Preparing Your Design for Display Printing
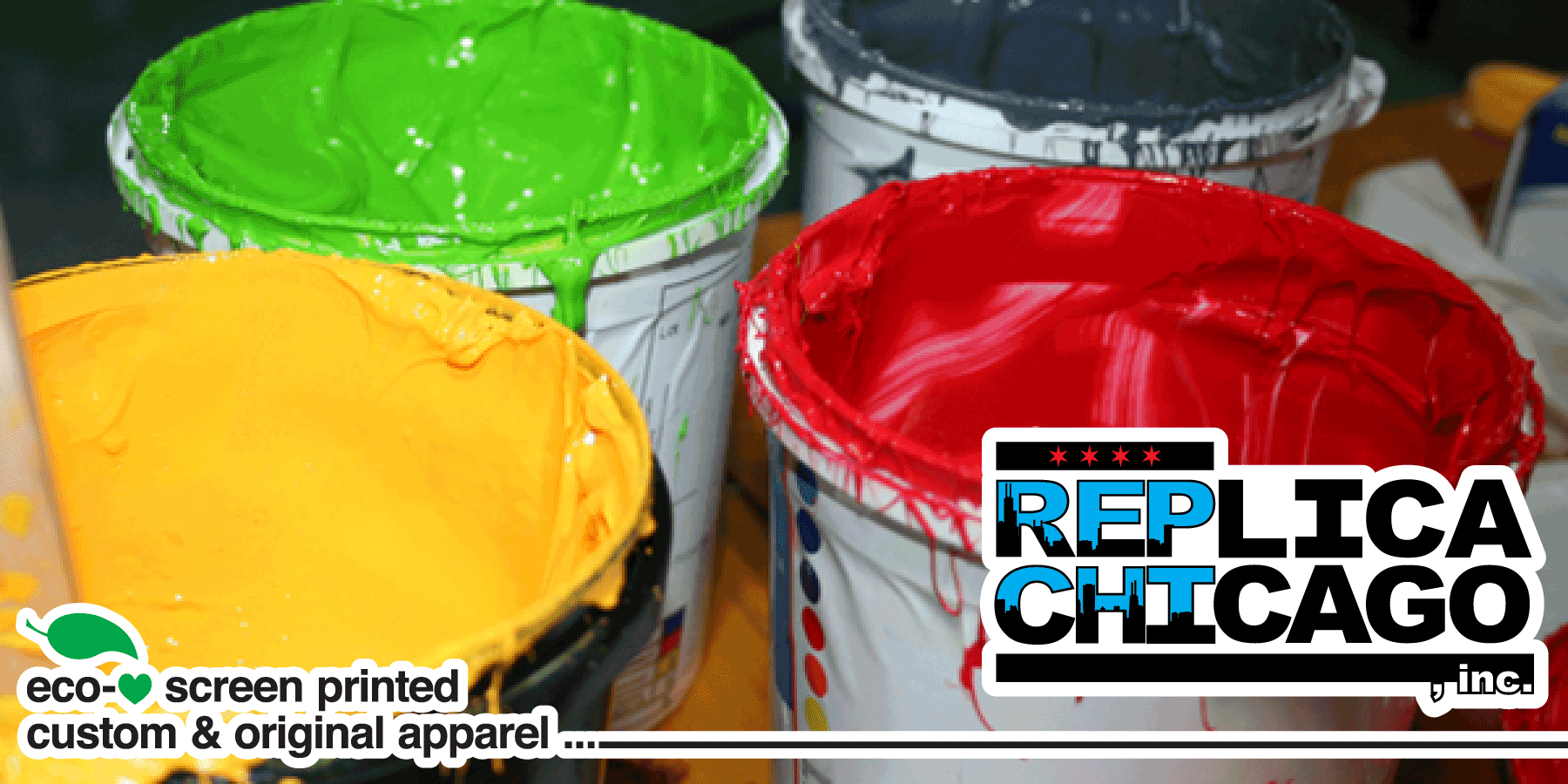
File Layout Needs
To guarantee your design looks dynamic and sharp on textile, you'll require to pay attention to submit layout needs for screen printing. Start with vector documents like AI or EPS, as they can be scaled without losing quality. If you utilize raster pictures, choose for high-resolution documents, such as TIFF or PNG, preferably at 300 DPI. Avoid making use of JPEGs, as they can lose clearness when resized. Additionally, see to it your style has a transparent background to stop undesirable white sides on your prints. Keep color modes in mind; CMYK is conventional for screen printing, so convert your RGB creates accordingly - screen printing kit. By following these guidelines, you'll establish your artwork up for an effective print.
Color Separation Methods
Shade separation is a vital step in preparing your layout for screen printing, and mastering it can considerably improve your print top quality. You'll need to damage your layout into individual colors, as each color requires a separate display during printing. Start by determining all the colors in your layout and produce layers for each one. You can make use of software application like Adobe Photoshop or Illustrator to isolate and separate colors efficiently. Be certain to conserve each layer as a separate file, normally in a layout like TIFF or PSD. This precision not only guarantees accurate color representation yet likewise improves the printing process. By taking notice of shade splitting up, you'll accomplish specialist and vivid cause your screen-printed garments.
Resolution and Size
Achieving the most effective lead to display printing begins with ensuring your layout has the right resolution and dimension. Ideally, your art work must go to least 300 DPI (dots per inch) for sharp, clear prints. Your final item may look pixelated and less than professional. if you utilize reduced resolution.
When it pertains to dimension, think about the dimensions of your print area. Style your art work to match the final print dimension, preferably developing it in the actual measurements you'll be publishing. This method, you'll prevent any type of unanticipated scaling problems.
Constantly inspect your layout in both vector and raster styles. Vector graphics can be scaled without losing high quality, making them ideal for screen printing. Preparing appropriately will assure your layout looks incredible on every garment!
Step-by-Step Screen Printing Process
Display printing is a vibrant procedure that allows you to create vivid styles on numerous surfaces. To get going, you'll need a screen, emulsion, and your selected ink. Prepare your screen by cleansing it thoroughly. Next off, use the emulsion evenly and allow it completely dry in a dark location. When completely dry, subject your screen to light with your style put on it, which will harden the solution where the light hits, producing a useful source stencil - screen printing kit.
After washing out the unexposed solution, your screen is all set. Set it up on your printing surface area and align your garment underneath it. Pour ink onto the screen and make use of a squeegee to press the ink via the pattern onto the material. Raise the screen carefully and allow the print completely dry. Lastly, treat the ink making use of heat to guarantee sturdiness. That's it! You've effectively display published your design.
Tips for Effective Display Printing Projects
While you're diving right into your screen printing jobs, bear in mind that prep work is essential to success. Begin by collecting all your products-- inks, screens, mops, and garments. A clean work space helps avoid undesirable errors, so clean up prior to you start.
Following, verify your art work is high-resolution and correctly sized for your garment. Evaluate your screen for appropriate direct exposure and clean it completely to avoid smudges. When mixing your inks, comply with the producer's guidelines to achieve the ideal consistency.
Throughout printing, use also pressure with your squeegee for constant results. Do not hurry; take your time to verify each print fulfills your criteria. After printing, let your garments completely dry completely prior to taking care of or packaging them.
Last but not least, always keep a sample of your work for future reference. By doing this, you can analyze your development and improve your strategies in time. Delighted printing!
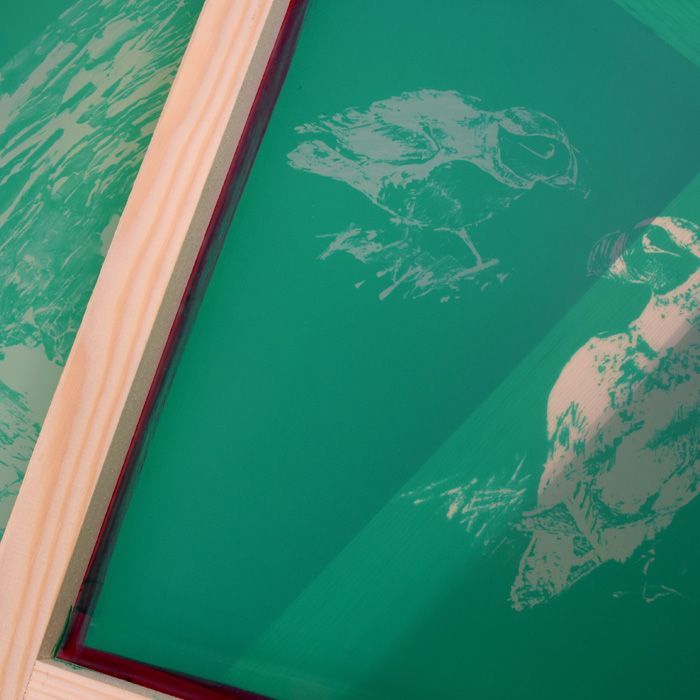
Often Asked Questions
Exactly how Long Does It Take to Set up a Display Printing Task?
Establishing a display printing job normally takes about thirty minutes to an hour. You'll prepare the displays, mix inks, and adjust the press. The time differs based on intricacy and experience, so stay arranged!
Can I Print on Various Fabric Enters Using the Very Same Technique?
Yes, you can print on different textile kinds utilizing the exact same method, however you'll require to adjust your inks and setups. Some fabrics take in ink in different ways, so exploring warranties the ideal outcomes for each and every material.
What Are Common Errors to Prevent in Display Printing?
When screen printing, avoid usual blunders like using the wrong ink, neglecting proper exposure times, or avoiding pre-press checks. Always check your configuration and keep clean displays to assure quality outcomes each time.
Exactly How Can I Appropriately Clean and Preserve My Display Printing Tools?
To correctly tidy and preserve your screen printing tools, you should frequently clean screens with appropriate solvents, inspect mops for wear, and guarantee all tools are kept dry and dust-free. Consistency boosts and avoids expensive repair services efficiency.
Is Screen Printing Environmentally Friendly Compared to Various Other Approaches?
Display printing can be a lot more environmentally pleasant than various other methods, especially if you utilize eco-conscious products and water-based inks. By selecting lasting supplies and practices, you minimize waste and decrease your effect on useful link the planet.
Screen Printing Uncovered: Whatever You Need to Know Regarding Tee Shirt and Garment Printing Methods
At its core, screen printing entails creating a stencil, or display, that allows ink to pass with only in particular areas. Position the display over the textile, then utilize a squeegee to push ink through the display onto the garment. One popular approach is standard display printing, where ink is pressed with a stenciled display.When picking inks and materials for screen printing, you need to take into account the type of ink that works best for your project.
Report this page